Robotics has become a game-changer in the manufacturing industry, bringing new levels of efficiency, precision, and automation. As we approach 2025, several robotics projects are set to revolutionize how products are made, assembled, and delivered. These innovative projects will streamline production, reduce labor costs, and improve the overall quality of goods. In this article, we will explore 10 robotics projects that will transform manufacturing in the next few years.
1. Collaborative Robots (Cobots) in Assembly Lines
Collaborative robots, or cobots, are designed to work alongside human workers in assembly lines. Unlike traditional robots, which require safety cages, cobots are built with safety features and can assist humans with tasks such as material handling, packaging, and quality control.
- Impact: Cobots improve efficiency and flexibility while allowing human workers to focus on more complex tasks.
- Example: Universal Robots’ UR series offers flexible and easy-to-deploy cobots for various manufacturing tasks.
2. Autonomous Mobile Robots (AMRs) for Material Handling
Autonomous Mobile Robots (AMRs) are transforming material handling by autonomously transporting raw materials, components, and finished products within manufacturing facilities. Equipped with sensors and AI, AMRs navigate and optimize material flow in real-time, improving efficiency in warehouses and production floors.
- Impact: Increased efficiency in material transport and reduced downtime.
- Example: Kivuto Technologies uses AMRs to manage inventory and move products within their manufacturing facilities.
3. 3D Printing for Custom Manufacturing
3D printing has already disrupted the manufacturing sector, and its impact will only grow in 2025. Robotic 3D printers enable rapid prototyping and the production of complex, customized parts with high precision. This technology is particularly valuable in industries such as aerospace, automotive, and healthcare.
- Impact: Faster production times and the ability to create highly customized products.
- Example: Stratasys’ robotic 3D printers are already being used in aerospace for creating intricate parts and components.
4. Robotic Welding Systems
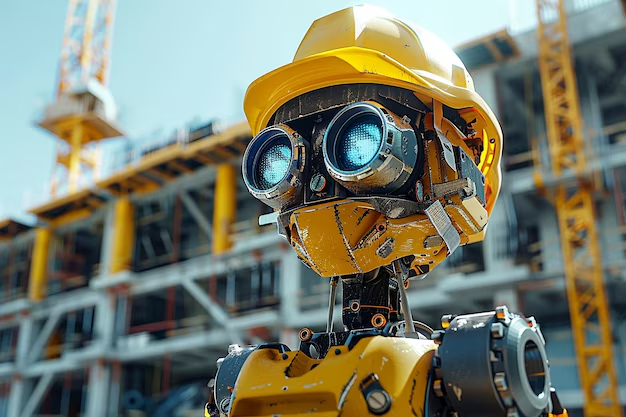
Robotic welding systems are set to play a huge role in the manufacturing industry by offering high precision and consistency in welding processes. These robots can perform complex welding tasks with speed and accuracy, reducing errors and improving the quality of welds.
- Impact: Increased efficiency, better weld quality, and reduced downtime.
- Example: FANUC’s Arc Mate series is designed for high-precision welding in automotive and heavy manufacturing sectors.
5. Robotic Quality Control and Inspection
Robots equipped with cameras and sensors are now capable of performing quality control and inspection tasks with higher accuracy than humans. These robots inspect products in real time, identifying defects and ensuring that manufacturing standards are met.
- Impact: Enhanced product quality and reduced human error.
- Example: Cognex Vision Systems offer robotic solutions for automated inspection in industries like automotive manufacturing.
6. Robot-Assisted Assembly
Robotic arms designed for robot-assisted assembly are capable of putting together complex parts with extreme precision. These robots work in tandem with human workers, providing assistance in tasks such as assembling electronic devices, machinery, and vehicles.
- Impact: Faster production times and reduced worker strain.
- Example: KUKA Robotics’ robotic arms are used in assembly lines to support the assembly of large machines and car components.
7. Predictive Maintenance Robots
Predictive maintenance robots will become crucial for minimizing downtime in manufacturing operations. These robots use AI, IoT sensors, and data analytics to monitor machinery and predict when maintenance is required, preventing equipment failure and reducing maintenance costs.
- Impact: Reduced unplanned downtime and extended equipment lifespan.
- Example: Uptake Technologies is integrating predictive maintenance technologies to anticipate equipment failures in manufacturing environments.
8. Robotic Paint Systems
Robots are increasingly used in painting applications, particularly in automotive manufacturing. Robotic paint systems offer consistent, high-quality finishes while reducing paint waste and improving safety by eliminating human exposure to hazardous chemicals.
- Impact: Better finish quality, reduced waste, and safer working conditions.
- Example: ABB’s robotic paint systems are widely used in automotive factories for precise and efficient painting processes.
9. Automated Packaging Systems
Automated packaging systems powered by robotics are changing how products are packaged in manufacturing plants. Robots can handle various packaging tasks such as filling, sealing, labeling, and palletizing products, speeding up the packaging process.
- Impact: Increased speed and efficiency in packaging operations.
- Example: Schneider Electric’s robotic packaging solutions automate packing, labeling, and palletizing in consumer goods manufacturing.
10. Robotic 3D Metrology for Precision Measurement
In manufacturing, precision is key. Robotic 3D metrology systems are being used to perform high-accuracy measurements of manufactured parts, ensuring that each component meets strict tolerances and quality standards.
- Impact: Higher precision in measurements, reducing defects and improving part compatibility.
- Example: Zeiss’ robotic metrology solutions provide automated 3D inspection for precision parts in industries such as aerospace and automotive.
Read More : http://Exploring the Future of Robotics: 10 Developments You Can’t Miss
Conclusion
The 10 robotics projects outlined above demonstrate the tremendous potential of robotics to revolutionize manufacturing in 2025. From autonomous material handling and robot-assisted assembly to predictive maintenance and quality control robots, these innovations will improve production efficiency, product quality, and worker safety. As robotics continues to evolve, manufacturers who adopt these cutting-edge technologies will be well-positioned for success in the highly competitive global market.